calcine rotary furnace
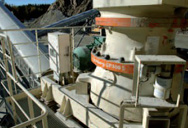
The effect of sulfur in rotary kiln fuels on nickel laterite
2020.10.1 The rotary kiln-electric furnace (RKEF) process is the primary method for extracting nickel from saprolite ores. In this technique, the ore is first calcined and pre
اObtener precio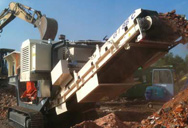
Inhibition of Sulfur Transfer from Fuel to the Calcine in Nickel ...
2022.1.20 A rotary kiln-electric furnace is the predominant process for producing ferronickel from nickel laterite ore. Fuel combustion in the rotary kiln generates sulfur
اObtener precio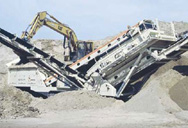
Fixing sulfur dioxide by feeding calcine oxide into the rotary ...
2023.1.20 The results extend the technology of in-furnace fixation for SO 2 in CFB coal-fired boilers to the rotary volatilization kiln in zinc smelting plant, providing new
اObtener precio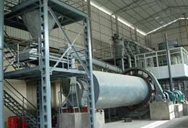
(PDF) Improving the rotary kiln-electric furnace process for ...
2021.9.16 The primary pyrometallurgical route to produce ferronickel from laterite nickel ores is the Rotary Kiln-Electric Furnace (RKEF) process. In the RKEF process,
اObtener precio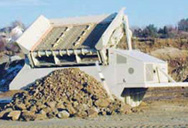
Large- and Particle-Scale energy assessment of
2022.7.1 This paper focuses on the rotary kiln furnace, an intermediate stage in which partially dried minerals convert into calcine, ready for smelting in an electric arc furnace.
اObtener precio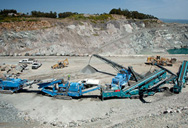
Simplification of the Calcine Transfer Control System
2022.11.27 ABSTRACT. The Rotary Kiln-Electric Furnace (RKEF) technology is the most commonly known method for processing rich nickel ore because of its
اObtener precio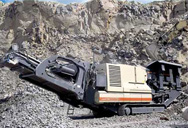
Data-driven classification of the chemical composition of calcine
2023.6.1 Raw ore is extracted from an open-pit mine, later classified into piles, dried out and pre-burned in a rotary kiln furnace to produce a base calcine that is then further
اObtener precio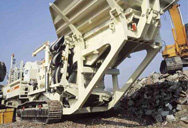
Improving the rotary kiln-electric furnace process for
2022.4.1 Here we refer to the calcined partially reduced mineral leaving the rotary kiln furnace as calcine. KPI1 and KPI2 reflect the main objectives of the dust insufflation
اObtener precio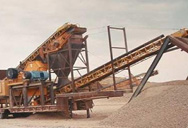
The Effect of Sulfur in Rotary Kiln Fuels on Nickel Laterite
2020.1.14 Rotary Kiln - Electric Furnace (RKEF) process is a pyrometallurgical technique to extract nickel from laterite ores. It is essentially a two-step process where
اObtener precio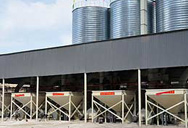
Sulfur deportment in nickel laterite calcination for ferronickel ...
The rotary kiln-electric furnace (RK-EF) process is a common pyrometallurgical route for ferronickel production from nickel laterite ores. Sulfur is a harmful impurity that
اObtener precio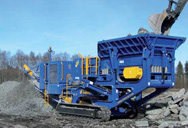
The Effect of Sulfur in Rotary Kiln Fuels on Nickel Laterite
2020.1.14 Rotary Kiln - Electric Furnace (RKEF) process is a pyrometallurgical technique to extract nickel from laterite ores. It is essentially a two-step process where the ore is first calcined in a rotary kiln and then smelted in an electric furnace. The product of the RKEF process is crude
اObtener precio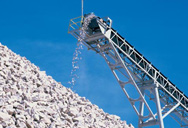
Schematics of the rotary kiln studied in this work. The
A recent study assessed the thermal and mechanical response of that rotary kiln furnace under transient operation [12]. Table 2 summarizes the chemical reactions and the corresponding standard ...
اObtener precio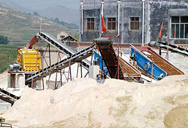
Fixing sulfur dioxide by feeding calcine oxide into the rotary ...
2023.1.20 Herein, feeding CaO into the rotary volatilization kiln as SO2-fixation agent is demonstrated to be an efficient in-furnace desulfurization strategy for zinc smelting plant. The sulfur distribution within the entire smelting process is systematically analyzed, determining that the critical procedure for pressuring the desulfurization system is ...
اObtener precio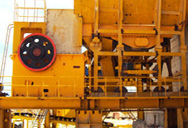
Modelling of Nickel Laterite Smelting to Ferronickel
2016.12.5 needed to remove it. The dried material, with some added coal, passes to rotary kilns where a flame heats the material. The coal volatiles and some of the fixed carbon partially reduce the ore. The remaining fixed carbon acts as the reductant in the following smelting step. Hot calcine is fed to an electric furnace (Figure 1b) where the ...
اObtener precio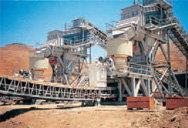
Data-driven classification of the chemical composition of calcine
2023.6.1 CMSA is a lateritic nickel ore extraction, mining and smelting operation with open-pit exploitation which began in 1982, producing 36,000 tons of ferronickel per year [1].Raw ore is extracted from an open-pit mine, later classified into piles, dried out and pre-burned in a rotary kiln furnace to produce a base calcine that is then further processed.
اObtener precio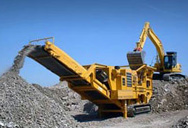
Metals Free Full-Text Nickel Laterite Smelting Processes
2019.9.3 The treatment of laterites has been a research hotspot in extractive metallurgy over the past decades. Industrially, the pyrometallurgical treatment of laterites is mostly accomplished with a well-established method, namely, the rotary kiln–electric arc furnace (RKEF) process, which includes three main operations—calcination,
اObtener precio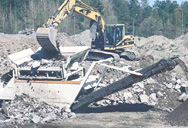
Calcination furnaces ovens manufactured by Carbolite Gero
Rotary Tube Furnaces TSR. Max temp: 1150 °C. Tube rotation 1.5 to 10 rpm. Single or 3-zone temperature control. Product details. Carbolite Gero furnaces and ovens are used for the thermal treatment process of calcination (or
اObtener precio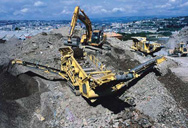
Production of Fe Ni by the rotary kiln-electric furnace process
1987.5.1 Rotary kiln-electric furnace (RK-EF) process is the main pyrometallurgical route for ferronickel production from nickel laterite ores. Coal is used as a common fuel for calcination of nickel laterites in rotary kiln. ... Higher sulfur deportation from the gas phase to the calcine was observed by raising the temperature from 600 to 800 °C ...
اObtener precio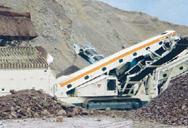
Three-dimensional computational fluid dynamics analysis of
2021.9.3 A computational fluid dynamics (CFD) method is proposed to analyze the operation of a submerged electric arc furnace (SAF) used in ferronickel production. A three-dimensional mathematical model ...
اObtener precio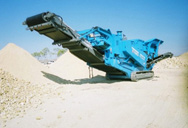
Furnace technology for ferro-nickel production -
2004.1.1 Abstract and Figures. This paper describes developments in ferro-nickel furnace technology, specifically improvements to cooling methods, furnace controls, and high voltage furnace operating ...
اObtener precio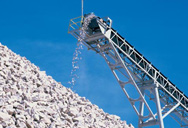
ESS Smelting Technology SpringerLink
2016.11.14 Drying, calcining, and solid-state reduction performed in shaft furnaces, rotary hearth furnaces, rotary kilns, fluidized bed furnaces, and so on are often followed by electric furnace smelting of the calcine. The system to transfer material to the smelting furnace often limits the temperature and degree of reduction that can be achieved during ...
اObtener precio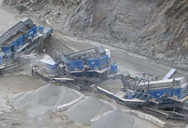
The diagram of material balance of the process of
The process of calcine production in rotary kilns at the Ferronikeli plant in Drenas is realized with great difficulties as a result of the formation of large adhesions in the areas of rotary kilns.
اObtener precio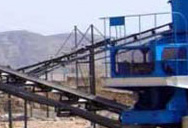
MATHEMATICAL SIMULATION OF THE PROCESS OF
2018.11.15 The furnace charge in the drum rotary furnaces is positioned in the form of a segment, adjacent to the rotat-ing side of the drum. The angle of segment chord inclination is close to the natural angle of repose of the pro-cessed materials and on average constitutes 27 to 35°. The drum cross-section is typically filled with the furnace
اObtener precio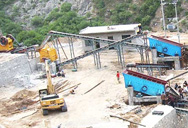
Future of Rotary Kiln - Electric Furnaces (RKEF) processing of
A paper by Walker et al. at the 2008 ALTA conference presented a future RKEF ferronickel facility that would utilise a high capacity (240 t/h calcine, 120 MW) rectangular electric furnace and the most productive rotary kilns available to date. At the time, kiln capacity did not match the furnace capacity and to support the operation of two 120 ...
اObtener precio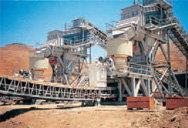
Considerations for Scale-Up of Ferronickel Electric
2016.11.9 further drying and calcination of the ore in rotary kilns, followed by smelting in large electric furnaces [termed the rotary kiln–electric furnace (RKEF) process] to produce a ferronickel product. Fifty years ago, the power rating on ferronickel electric furnaces was 10 MW. The industry has advanced significantly since then, with power ...
اObtener precio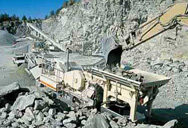
Energy Balance Diagram of the Rotary Kiln (R/K)-Electric Furnace
Download scientific diagram Energy Balance Diagram of the Rotary Kiln (R/K)-Electric Furnace (E/F) System (Based on 100 t of Rotary Kiln Calcine or 104.9 t of Natural Laterite) from publication ...
اObtener precio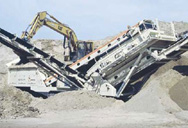
Production of ferronickel from nickel laterites in a DC arc furnace
Example 2 - 120 kW test . A 120 kW DC-arc furnace was used for the processing of laterite calcine blends, with the objective being the study of the smelting behaviour of materials with SiO 2 /MgO ratios ranging from 1.2 to 3.0. The smelting of laterite types having a range of Fe contents from 15 to 20% was tested at the same time. A part of the test was devoted
اObtener precio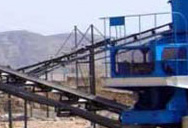
Magnesium Smelting via the Pidgeon Process SpringerLink
2021.4.30 At present, it is common in Japan to use a rotary kiln in silicothermic magnesium smelting to calcine dolomite. Japan Tazawa Industry Co., Ltd., ... Dolomite is heated to 1100–1200 °C in a rotary furnace (rotary kiln) or shaft kiln to form calcined dolomite (MgO CaO). The specific process is as follows: After the calcined dolomite is ...
اObtener precio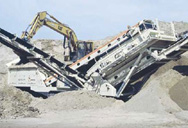
(PDF) OPTIMIZATION OF TECHNOLOGICAL FE-NI
2013.7.14 The new Rotary Kiln calcine has about 3.89% more to tal Iron as a result of increasing the portion of Albanian ores in the Rotary Kiln feed. Consequently the slag produced in the Electr ic furnace
اObtener precio>> Next: Jun Trituradoras De Piedra De Potencia
Mas noticias
- equipo de fundición de cobre
- Maquinas Moledoras Productos
- suministro de mineral de hierro
- gran trituradora de barita comercial
- cebada trituradora de rodillos ajuste
- equipo de clasificacion de espiral doble mineral
- trituradoras de impacto bien
- hierro plantas de beneficio de minera en china llave en mano
- especificacin cenit trituradora de piedra
- capacidad de molinos de bolas de 6 pies por 6 pies
- mina de carbón chancadora de martillo
- diseno de trituradora de arcilla
- molinos portatil para moler mineral
- de laboratorio trituradora de martillos para el suministro
- mejor diseno para trituradora de piedra
- trituradora de cono marca
- Prototipos de chancadoras de basura
- procesamiento del oro en rocas molino de barras
- molienda tipos de molino
- Hecho De Henan Trituradora De Impacto
- chancadora de piedra espa a vendo usado
- cubo de elevador de granos
- trituradora de mandíbulas para la arena que hace la planta artificial
- foacutermula de fosfato de hierro
- proceso de planta de cemento fotos de diagrama de flujo
- equipo profesional de extraccion de mineral de oro de
- pra y venta chancadora de piedra
- acm 60 used mill hosokawa colombia
- chancadora de piedra máquina de pearson
- la oficina mco catastro minero