grinding mills of minerals
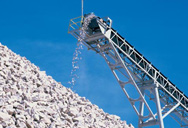
Grinding mills - for mining and minerals processing - Metso
Metso Select™ horizontal grinding mills are a pre-engineered range of class-leading horizontal grinding mills, designed from industry leading experience and expertise. The pre-engineered package eliminates time and costs usually spent in the engineering and
اObtener precio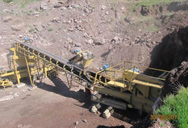
Mill (grinding) - Wikipedia
In materials processing a grinder is a machine for producing fine particle size reduction through attrition and compressive forces at the grain size level. See also crusher for mechanisms producing larger particles. In general, grinding processes require a relatively large amount of energy; for this reason, an experimental method to measure the energy used locally during milling with di
اObtener precio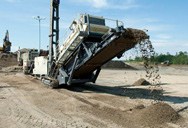
A process mineralogy approach to study the efficiency of
2020.12.3 Crushing and grinding processes are typically used by crushers and mills to liberate minerals, which are energy-intensive processes (especially fine grinding by mill).
اObtener precio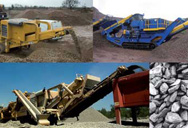
Mineral processing Metallurgy, Crushing Grinding
Hand sampling is usually expensive, slow, and inaccurate, so that it is generally applied only where the material is not suitable for machine sampling (slimy ore, for example) or where machinery is either not
اObtener precio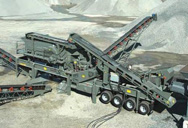
A Review of the Grinding Media in Ball Mills for Mineral Processing
2023.10.27 In mineral processing, grinding, which is key to the liberation of valuable minerals from gangue, is achieved in primary, secondary and tertiary applications as well as regrind mills. These mills are further categorized by the nature of the discharge configuration: trunnion overflow mills operated in open or closed circuits or grate
اObtener precio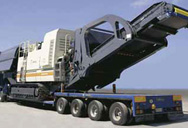
Variables affecting the fine grinding of minerals using
2003.4.1 The most commonly used stirred mills in the minerals processing industry are: Tower mill: Manufactured in Japan by Kubota. It was the first low speed stirred mill applied in the minerals industry.
اObtener precio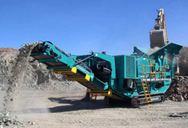
Energy Use of Fine Grinding in Mineral Processing
2013.12.18 Grinding activities in general (including coarse, intermediate, and fine grinding) account for 0.5 pct of U.S. primary energy use, 3.8 pct of total U.S. electricity consumption, and 40 pct of total U.S. mining industry energy use. Large energy saving opportunities have been identified in grinding in particular. [ 1]
اObtener precio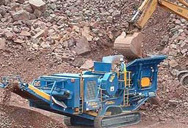
Chapter 7. Grinding Mills - Wills' Mineral Processing Technology,
According to the ways by which motion is imparted to the charge, grinding mills are generally classified into two types: tumbling mills and stirred mills. In tumbling mills, the mill shell is rotated and motion is imparted to the charge via the mill shell. The grinding medium may be steel rods, balls, or rock itself.
اObtener precio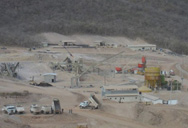
Variables affecting the fine grinding of minerals using
2003.4.1 Base metal resources are becoming more fine-grained and refractory and minerals separation processes require these ores to be milled to increasingly finer sizes. To cope with very fine grinding to below a P 80 of approximately 15
اObtener precio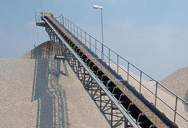
Variables Affecting the Fine Grinding of Minerals Using Stirred Mills
2003.4.1 Neither this technology, nor the basic concepts of fine grinding, are well understood by the minerals processing industry. ... mills. Minerals Engineering 14, 1177–1186, Special issue from MEI.
اObtener precio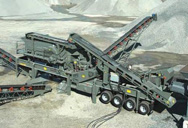
Mineral processing - milling
expensive maintenance requirement. Most types of readily available hammer mills for agricultural grinding are not suitable for grinding most types of minerals. Hardness of minerals is expressed on Mohs scale - a numerical index ranging from 1 for talc (the softest mineral) to 10 for diamond (the hardest known material). Table 2 below shows
اObtener precio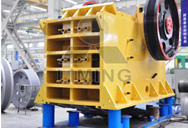
Improving Energy Efficiency Across Mineral Processing and
grinding mills and froth flotation cells in the same circuit arrangement as would be used in a full-scale industrial plant. Energy consumption during each of the grinding stages is monitored and recorded using an energy metre. A typical process flow sheet with two stages of comminution and separation is
اObtener precio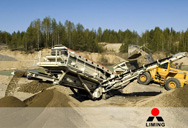
Grinding SpringerLink
2022.2.28 Therefore, the grinding media do not fall on the mineral particles, and grinding does not occur. Generally, the critical rotational speed in ball mills is around 4 m/s [ 103 ]. However, the mechanism applied in stirred milling overcomes this limitation.
اObtener precio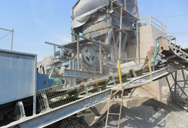
MINERAL PROCESSING - MILLING - United Diversity
requirement. Most types of readily available hammer mills for agricultural grinding are not suitable for grinding most types of minerals. Hardness of minerals is expressed on Mohs scale - a numerical index ranging from 1 for talc (the softest mineral) to 10 for diamond (the hardest known material). Table 2 below shows Mohs’ scale of hardness.
اObtener precio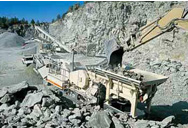
Energy Use of Fine Grinding in Mineral Processing
2013.12.18 Fine grinding, to P80 sizes as low as 7 μm, is becoming increasingly important as mines treat ores with smaller liberation sizes. This grinding is typically done using stirred mills such as the Isamill or Stirred Media Detritor. While fine grinding consumes less energy than primary grinding, it can still account for a substantial part of
اObtener precio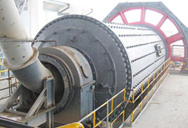
Metals Free Full-Text Kinetics of Dry-Batch Grinding in a ... - MDPI
2020.12.17 In the mining industry, the comminution stage can represent up to 70% of the energy consumed in a mineral processing plant [1,2,3,4,5].With ball-mill grinding being one of the most energy-consuming techniques, setting the optimal values of the operational and mineralogical parameters for efficient grinding is a key target in mineral processing
اObtener precio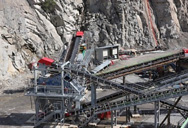
SAG vs. AG Mills: Understanding the Key Differences - ball mills
SAG mills use a combination of steel balls and rock particles as grinding media, while AG mills use only the ore itself. Both types of mills are used for grinding ore in mineral processing operations, but SAG mills are larger in size and can grind larger quantities of ore. AG mills, on the other hand, are smaller and are typically used for ...
اObtener precio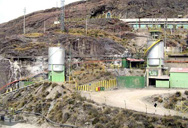
Key considerations when selecting a mill lining system Weir
In the past, grinding mills were typically lined with cast metal linings of varying steel or iron alloys, and lining system selection was typically driven by level of wear protection and cost. ... Weir Minerals has more than 40 years of experience in designing and
اObtener precio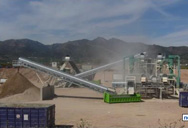
(PDF) SIZE REDUCTION BY GRINDING METHODS - ResearchGate
2017.3.4 Rod mills are less common than ball m ills for grinding minerals. The rods used in the mill, usually a high-carbon steel, can vary in both the length and the diameter.
اObtener precio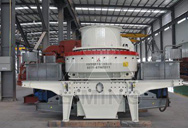
Minerals Free Full-Text Performance Comparison of the ... - MDPI
2023.1.31 Stirred media mills are indispensable members of the mineral processing flowsheets, which are requiring regrind and fine grinding applications. Such a high utilization of these technologies comes from their energy-efficient operation over the conventional techniques for below the size range of 100 micron [1,2,3,4].
اObtener precio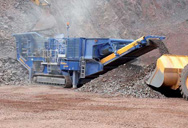
(PDF) Grinding Media in Ball Mills-A Review
2023.4.23 It consumes most of the energy used in mineral processing plants with grinding using up to 50% of the provided energy. Tumbling mills are an old technology that is still commonly used for
اObtener precio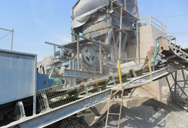
Breaking down energy consumption in industrial
2017.1.17 Abstract and Figures. Grinding mills are infamous for their extremely low energy efficiency. It is generally accepted that the energy required to produce new mineral surfaces is less than 1% of ...
اObtener precio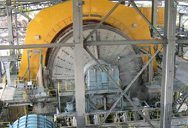
INDUSTRIAL MINERALOGY: MINERAL PROCESSING,
etc. (semi autogeneous). Autogeneous grinding mills do not use the grinding bodies. In roll crushers, the crushing and grinding are combined together where two cylinders mounted as horizontal shafts drive in opposite directions. When the cylinders are pressed under high pressure, disintegration operation of the materials between the cylinders ...
اObtener precio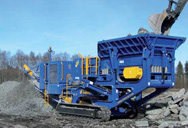
Consumption of steel grinding media in mills – A review
2013.8.1 A complicating factor in accounting for the effects in these galvanic cells is that the effects of galvanic interactions between sulphide minerals and grinding media need to be considered in conjunction with the galvanic interactions that can occur between sulphide minerals, as discussed by Rao and Finch, 1988, Cheng and Iwasaki, 1992,
اObtener precio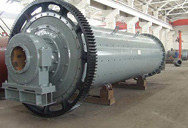
Modeling and prediction of wear rate of grinding media in mineral ...
2020.8.3 The grinding media wear plays an important role in the economics of grinding processes in mineral processing plants. Wear is defined as a progressive loss of material from a solid body owing to its contact and relative movement against a surface [].It has been accepted that wear is resulted in a lower the operational efficiency of
اObtener precio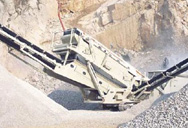
Quantifying the energy efficiency of fine grinding circuits
2021.11.25 The ball mill was grinding to a P 80 of 50 to 70 µm, therefore the traditional marker ... K., 1988. A first survey of grinding with high-compression roller mills. International Journal of Mineral Processing 22, 401-412. Palaniandy, S., Halomoan, R., Ishikawa, H., 2018. Shifting the comminution workload from the primary ball ...
اObtener precio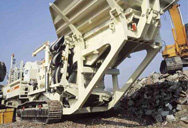
Consumption of steel grinding media in mills – A review
2013.8.1 In this study, the current understanding of the factors affecting the consumption of steel media in comminution systems in mineral processing are reviewed, together with models predicting wear losses in grinding media. Media wear arises as a consequence of complex interaction between a range of variables related to processing
اObtener precio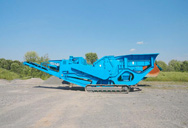
Grinding mills: how to accurately predict their power draw
2003.10.3 This is a material transport problem and in the case of grinding mills it is usually sufficient to assume that if the machine can draw the required power it can also process the required ...
اObtener precio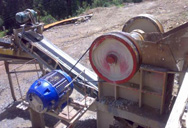
Grinding Mills — Types, Working Principle Applications
2018.8.17 Rod Mills — these rotating mills use rods for grinding media causing friction and attrition between steel rods and ore particles. Rod mills can accept feed up to approximately 50 mm. (2 in.) and ...
اObtener precio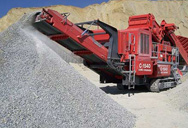
Variables affecting the fine grinding of minerals using stirred mills ...
2003.4.1 Ultrafine grinding for improved mineral liberation in flotation concentrates. J. Parry. Engineering, Materials Science. 2006. As the minerals industry is required to process increasingly complex, finely-grained ores, stirred mills are replacing ball mills for regrind applications in flotation circuits. Stirred mills are.
اObtener precioMas noticias
- molino de bolas y vrm comparacion
- Trituracin de carbn y proceso de seleccin
- molino de la amoladora ukuran
- remolque moacutevil de chancado de la planta
- chancadora de tecnologia de cuarzo
- el molino decadencia
- world best gold detectors
- estado de costo de produccion y ventas mexico
- Plantas trituradoras méxico
- máquina trituradora de piedra cono 3 pies
- separacion del oro de la arena
- piedra caliza imagenes de archivo
- proveedores de linea de produccion de beneficio de grundfos
- outotec precio de la maquina de sinter
- trituradora de piedra duración
- trituradora de piedra coste de produccion
- oro maquina del fabricante de la cadena
- pdf epub del el invierno del mundo libre
- molienda de molino de bola máquina molino para el cuarzo
- Trituradora de áridos en Argentina
- molinos para nixtamal en cd matamoros tamaulipas
- molino de martillos Stedman un 3024
- china mejor proveedor molino
- cilindro de molino en colombia
- trituradoras de caliza
- Combinado de carbón chancadora de y mezclador
- picadora o molino de carne congelad
- Pengasah Piedra de pulir
- trituradora de quijada city track ct 80
- temperaturas rodillos de molienda