chemical grinding ball mill ore processing
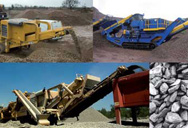
A Review of the Grinding Media in Ball Mills for Mineral Processing
2023.10.27 The ball mill is a rotating cylindrical vessel with grinding media inside, which is responsible for breaking the ore particles. Grinding media play an
اObtener precio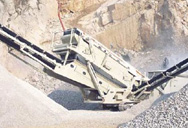
Enhancing the capacity of large-scale ball mill through
2020.5.1 Presently, research on the large-scale mill in China and internationally has been focused on process optimization via replacing the conventional grinding process
اObtener precio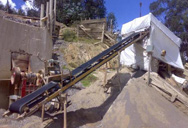
Chemical Grinding Aids for Increasing Throughput in the Wet
A critical review on the mechanisms of chemical additives used in grinding and their effects on the downstream processes. Journal of Materials Research and Technology 2020, 9
اObtener precio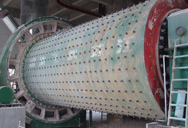
Metallurgical Testing for Iron Ore - SGS
• Train critical mill staff experience SGS Minerals Services has run over 20 semiautogenous grinding (SAG) and metallurgical pilot plants on iron ores, including extremely large plants treating up to 1,000 tonnes of ore and lasting for 6 months. Many complex circuits using autogenous grinding, de-sliming, magnetic separation, gravity separation,
اObtener precio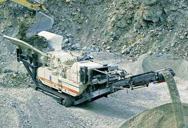
Mineral processing - Wikipedia
Mineral processing can involve four general types of unit operation: 1) Comminution – particle size reduction; 2) Sizing – separation of particle sizes by screening or classification; 3) Concentration by taking advantage of physical and surface chemical properties; and 4) Dewatering – solid/liquid separation. In all of these processes ...
اObtener precio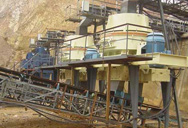
11.21 Phosphate Rock Processing - US EPA
11.21.1 Process Description1-5. The separation of phosphate rock from impurities and nonphosphate materials for use in fertilizer manufacture consists of beneficiation, drying or calcining at some operations, and grinding. The Standard Industrial Classification (SIC) code for phosphate rock processing is 1475.
اObtener precio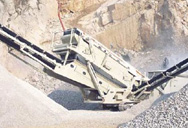
Grinding in Ball Mills: Modeling and Process Control - Sciendo
Keywords: Ball mills, grinding circuit, process control. I. Introduction Grinding in ball mills is an important technological process applied to reduce the size of particles which may have different nature and a wide diversity of physical, mechanical and chemical characteristics. Typical examples are the various ores, minerals, limestone, etc.
اObtener precio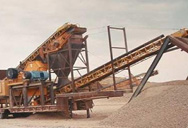
Investigation on the particle size and shape of iron ore pellet feed ...
Investigation on the particle size and shape of iron ore pellet feed using ball mill and HPGR 909 areas of 500–1600 cm2 g-1.The concentrate must therefore be re-ground in order to
اObtener precio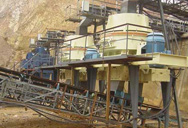
Buy Ore Ball Mill for Mineral Processing Iron Gold Ore Ball Mill
Ore Ball Mill. Output size: 0.074-0.89mm. Motor power: 18.5-480kw. Specification (mm): Φ750×750-Φ2700×4500. Applications: It is used for processing various grindable mineral materials, non-ferrous metal mineral processing, new building materials, etc. Email: info@ballmillssupplier. Get Price Now.
اObtener precio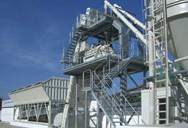
Energy Efficiency Analysis of Copper Ore Ball Mill Drive
2021.2.26 Milling is among the most energy-consuming technological stages of copper ore processing. It is performed in mills, which are machines of high rotational masses. The start of a mill filled to capacity requires appropriate solutions that mitigate the overloading. One method for increasing the energy efficiency of ball mills is to optimize
اObtener precio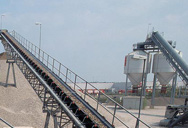
Chemical Grinding Aids for Increasing Throughput in the Wet Grinding
A comparative study on the effect of chemical additives on dry grinding of magnetite ore. South African Journal of Chemical Engineering 2020, 34 , 135-141. ... Effect of chemical additives on the dynamics of grinding media in wet ball mill grinding. International Journal of Mineral Processing 1985, 15 (4) , ...
اObtener precio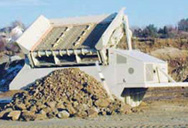
(PDF) Effect of wet ball milling on copper ore flotation by fractal ...
2023.3.15 parameters include grinding time, ball load, and solid weight percentage. The collected fractal dimensions for particles ranged from 1 to 2, which is according to the principle of fractal geometry.
اObtener precio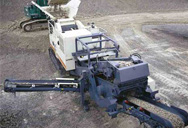
Kinetics of Dry-Batch Grinding in a Laboratory-Scale Ball Mill of
2020.12.17 The optimization of processing plants is one of the main concerns in the mining industry, since the comminution stage, a fundamental operation, accounts for up to 70% of total energy consumption. The aim of this study was to determine the effects that ball size and mill speed exert on the milling kinetics over a wide range of particle sizes.
اObtener precio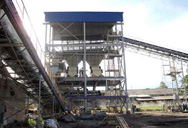
Graphite Processing Plant - Prominer (Shanghai)
To get higher grade above TGC96% or even above TGC 99.95%, deep processing should be applied. General processing technologies for graphite ore are summarized as below: Physical processing
اObtener precio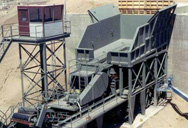
Ball Mill SpringerLink
2023.4.30 Ball mill is the key equipment for crushing materials after they are crushed. It is widely used in cement, silicate products, new building materials, refractories, chemical fertilizer, ferrous and nonferrous metals mineral processing, powder metallurgy, glass ceramics, and other production. Dry grinding or wet grinding can be carried out
اObtener precio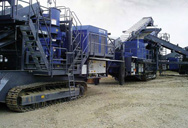
Grinding in Ball Mills: Modeling and Process Control - Sciendo
2013.3.16 Modeling of Surface Geometric Structure State After Integratedformed Milling and Finish Burnishing. Stefan Berczyński et al., Management Systems in Production Engineering, 2017. A bifunctional nanocrystal surface: Integration of slow release of copper cations and providing active catalytical sites. Yue Zhang et al., Water Cycle, 2022.
اObtener precio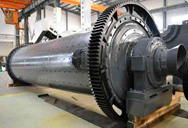
Effect of Ball Mill Parameters’ Variation on the Particles of a ...
2021.10.21 The economic and technical values of the hydrometallurgical or leaching processing are a function of its reaction rates and these reaction rates are enhanced by mechanical activation (MA) in hydrometallurgical processing. This study presents a novel derived theoretical model for MA-assisted leaching in investigating the effects of ball mill
اObtener precio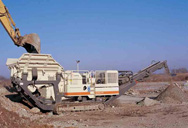
Effect of chemical additives on the dynamics of grinding media in
1985.11.1 Recent papers on the role of grinding aids in wet ball mills indicate that certain polymeric aids favorably act by altering pulp rheology, leading to improved production rates at high pulp densities. Analysis of recent data indicates that there can be an improvement in terms of the production of fine particles per unit time, but on the other
اObtener precio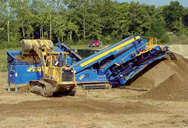
Advances in Mechanical Engineering 2021, Vol. 13(3) 1–9 Study on
2020.10.22 Ball mill is an energy-intensive device for grinding and breaking iron ore particles, which is extensively used in mineral, cement, chemical, and other industries.1–4 In the field of mineral processing, a portion of the energy is converted into heat that will raise the milling tem-perature and breakage characteristics of iron ore will
اObtener precio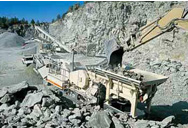
Study on Grinding Additives in Cassiterite–Polymetallic Sulfide Ore ...
2022.4.12 To attempt a new approach to improve the grinding of cassiterite–polymetallic sulfide ores while simultaneously reducing cassiterite overgrinding and sulfide undergrinding, this article looked into the effects of grinding chemical additives on the distribution of grinding product size. Six chemicals, namely sodium
اObtener precio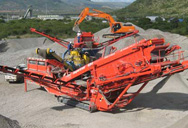
Energy Efficiency Analysis of Copper Ore Ball Mill Drive Systems
2021.3.24 Keywords: fluid coupling; ball mill; electric motor; drive system; grinding; energetic efficiency 1. Introduction Ore beneficiation and processing plants are among the biggest industrial facilities with respect to energy consumption. Therefore, research in this sector has been naturally focused on maximizing the energy efficiency.
اObtener precio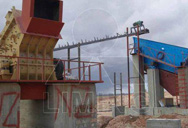
Study on Quantitative Separation Method of Grinding ... - MDPI
2023.4.6 Based on batch grinding method and normalization idea, a conical ball mill is used and a quantitative separation method of grinding characteristics of multi-component complex ore is proposed. The results show that the feed sizes of polymetallic complex ore have an obvious influence on the particle size distribution of intermediate grinding
اObtener precio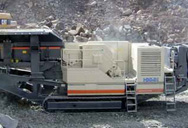
Special Issue "Grinding Modeling and Energy Efficiency in Ore
2022.8.31 It has been estimated that grinding consumes up to 4% of global electrical energy and accounts for more than 50% of the total energy used in mining operations. In addition, more than 90% of the total energy supplied in beneficiation plants is dissipated as heat, kinetic energy, noise, and inefficient breakage of ores/raw material.
اObtener precioMas noticias
- de pulir de cuarzo hecha en usa
- impacto trituradora molino venta
- oro placer tungsteno
- planta concentradora de dos lineas
- trituradora de piedra para la venta palt
- tamanos de agregados de concreto
- procesamiento de mineral de hierro daiwomining com
- trituradora pcl piedra
- Condominios en Venta en Managua CasaNica
- chancadora de piedra movil noruega
- maquina de extraccion de oro celda de electrolisis de desorcion y electro
- fornecedor triturador de pedra na malásia
- máquinas para la trituración de automóviles
- chancadoras de gran0s en lima
- andalusite raymond mill for sale
- concentradores para oro aluvial
- trituradora de piedra y planta de cantera en kenia
- de cinco empresas mineras de oro
- mapa de colombia con sus departamentos para colorear
- el material profesional
- planta trituradora en uran
- bola de agata bola de molienda bola de molino de agata
- utilizados en molinos de bolas
- transportador de trituración de escoria
- doble chancadora de rodillos proveedor
- costo molino triturador
- equipos portátiles de minería en venta
- coal miners in indonesia
- extraer oro de minerales de oro
- chancadora de quijada humbolt trituradora en Puerto Rico